How To Control The Output Particle Size Of The Aggregate Crushing Plant?
- retrospect1208
- 2024年4月15日
- 讀畢需時 3 分鐘
Controlling the particle size of aggregates produced by a crushing plant is crucial for achieving desired specifications and optimizing the performance of construction materials. Whether for road construction, building projects, or concrete production, the particle size distribution of aggregates directly impacts the strength, durability, and workability of the final product. Therefore, understanding and implementing effective methods to control the output particle size is essential for ensuring quality and consistency in construction projects.
Methods for Controlling Output Particle Size
Adjusting the Crusher Settings
The primary method for controlling the output particle size of an aggregate crushing plant is by adjusting the settings of the crusher. This involves modifying the parameters of the crushing equipment to regulate the size of the final product. Key settings that can be adjusted include the stone crushing machine's gap setting, speed, and eccentric throw.
Gap Setting: The gap setting refers to the distance between the crusher's mantle and concave, which determines the size of the crushed material. By adjusting the gap setting, operators can control the size of the output material. A smaller gap results in finer particles, while a larger gap produces coarser aggregates.
Speed: The rotational speed of the crusher's eccentric shaft can also influence the particle size distribution. Higher rotational speeds typically result in finer particle sizes, while lower speeds produce coarser aggregates. Adjusting the crusher's speed allows operators to fine-tune the crushing process to meet specific requirements.
Eccentric Throw: The eccentric throw, or the distance that the crushing head moves during operation, affects the compression and crushing action within the crushing chamber. By modifying the eccentric throw, operators can regulate the size of the crushed material. Increasing the eccentric throw can lead to finer particles, while reducing it produces coarser aggregates.
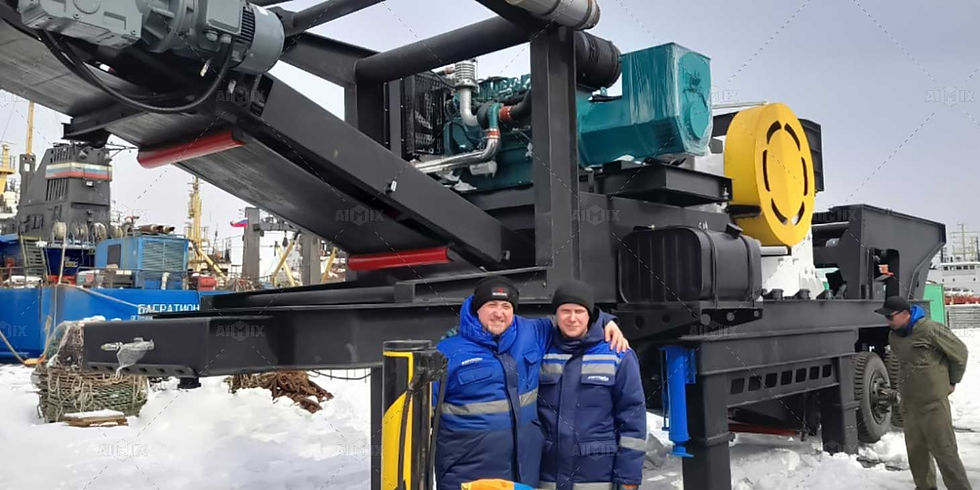
Using Screening Equipment
In addition to adjusting crusher settings, screening equipment can also be used to control the output particle size of an aggregate crushing plant. Screening involves separating the crushed material into different size fractions using screens or sieves. This allows operators to remove oversized or undersized particles and ensure that the final product meets desired specifications.
Screening Process: The screening process typically involves passing the crushed material through a series of screens with progressively smaller openings. As the material moves through the screens, particles that are smaller than the screen openings pass through, while larger particles are retained. By selecting screens with appropriate opening sizes, operators can control the size distribution of the output material.
Multiple Deck Screens: Some screening equipment features multiple decks, each with different screen openings. This allows for more precise control over the particle size distribution by separating the material into multiple size fractions simultaneously. By strategically arranging the screens and adjusting the deck angles, operators can optimize the screening process for desired results. Learn more here: https://aimixcrusherplant.com/rock-crusher-sale/.
Implementing Additional Crushing Stages
Another method for controlling the output particle size of an aggregate crushing plant is by implementing additional crushing stages. This involves passing the crushed material through multiple crushers or stages of crushing to further reduce the size of the aggregates. Each additional crushing stage allows for finer particle size reduction and greater control over the final product.
Primary, Secondary, and Tertiary Crushing: Aggregate crushing plants often utilize primary, secondary, and tertiary crushers to achieve the desired particle size distribution. Primary crushers initially break down the raw material into coarse fragments, which are then further reduced in size by secondary and tertiary crushers. This multi-stage crushing process enables operators to produce aggregates with precise particle size specifications.

Impact of Crushing Equipment: The selection of crushing equipment for additional crushing stages depends on factors such as the hardness and abrasiveness of the material, desired particle size distribution, and production requirements. Cone crushers, impact crushers, and gyratory crushers are commonly used in secondary and tertiary crushing stages, each offering unique advantages in terms of particle size control and efficiency.
Conclusion
Controlling the output particle size of an aggregate crusher plant is essential for ensuring the quality and performance of construction materials. By adjusting crusher settings, using screening equipment, and implementing additional crushing stages, operators can achieve precise control over the size distribution of aggregates. This not only enhances the quality of the final product but also improves the efficiency and productivity of construction projects. With a thorough understanding of these methods, operators can optimize the crushing process to meet specific requirements and achieve superior results in various applications.
Comments